【課題解決】射出成形品の静電気除去でホコリの付着を防止
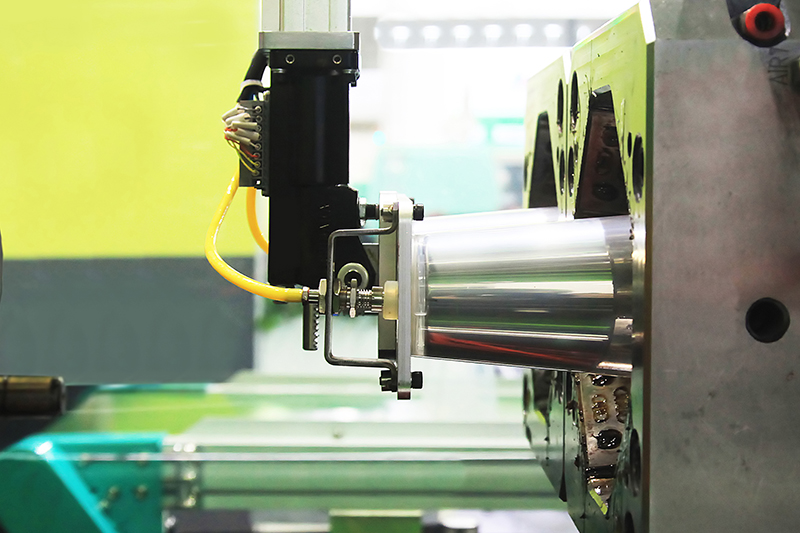
射出成形機から成形品を取り出す「取り出し機」。プラスチック成形のオートメーションに必須の自動化設備ですが、高い品質が求められるレンズ部品などの射出成形では、ホコリの付着による品質低下が問題となっていました。
この記事では樹脂成形工場における、射出成形品の取り出し工程でのお困りごとをご紹介します。
射出成形品の静電気によるホコリの課題
従来、射出成形機の自動化ラインでは、「取り出し機」を使いプラスチック成形品を取り出します。
しかし成形品を取り出して搬送する間に、ホコリが付着することがありました。
また帯電した静電気によって空気中のホコリを引き付けてしまい、あとからイナズマのような放電跡(スタティックマーク)が現れたり、「吸着パッドの痕」が浮き出てくるようなことも….
現場では、いかに射出成形品に帯電した静電気を取り除き、ホコリの付着や、清掃・洗浄などの後工程の手間をなくすかが課題となっていたのです。
POINT課題のポイント
- 静電気によるホコリの付着で困っている
- 清掃・洗浄などの後工程の手間をなくしたい
射出成形品のホコリの付着を「イオナイザー」で解決
静電気の原因は、金型と樹脂が擦れあうことで発生する「摩擦帯電」と、成形品を取り外す際に発生する「剥離帯電」にあります。静電気は目に見えないため、自動化の進んだ工場でも対策が後回しになってしまうことが少なくありません。
そこで採用されているのが「ノズル型イオナイザー」です。
「静電気除去ピンポイントノズル〈N-3〉」は、軽量コンパクトなノズル型のイオナイザー。チャック盤の稼働プログラムに合わせて、各工程でイオン化されたエアを噴射することで静電気を除去し、ホコリを寄せ付けない搬送ラインを作ることができます。
①チャック盤の挿入時
②チャック盤による搬送時
③コンベアへの積載時
プラスチックレンズの成形工場では、成形品の除電により「組み立て時のゴミやホコリの混入がなくなった!」「ブツ(ゴミ、ホコリの混入)を防止するため行なっていた目視検査や洗浄などの手間がなくなり、生産性が向上した!」などとの声も。小さなホコリが大敵な精密部品や透明部品の自動化設備でも採用されています。
重量104gと軽量・コンパクト。吸着パッドやチャックパーツ、エアーニッパーなどが多数取り付けられたチャック盤にも複数取り付けができ、ワイドノズルによる広範囲の除電も可能です。
射出成形品のホコリの付着防止で、現場の生産性向上におこたえします。
POINT解決のポイント
- イオナイザーによる除電で、ホコリの付着を防止
- 清掃・洗浄などの後工程がなくなり、生産性向上が実現
関連商品
お問い合わせフォーム
本記事についてのお問い合わせは、下記のフォームからご連絡ください。
課題解決事例は課題解決のための皆様の「気付き」となればと考えています。更なる改善案などがございましたら是非とも共有させていただきたいと存じます。
掲載に関しては都度、ご確認の上追加掲載させていただきます。