【課題解決】フィルム裁断時の静電気除去で品質向上が実現
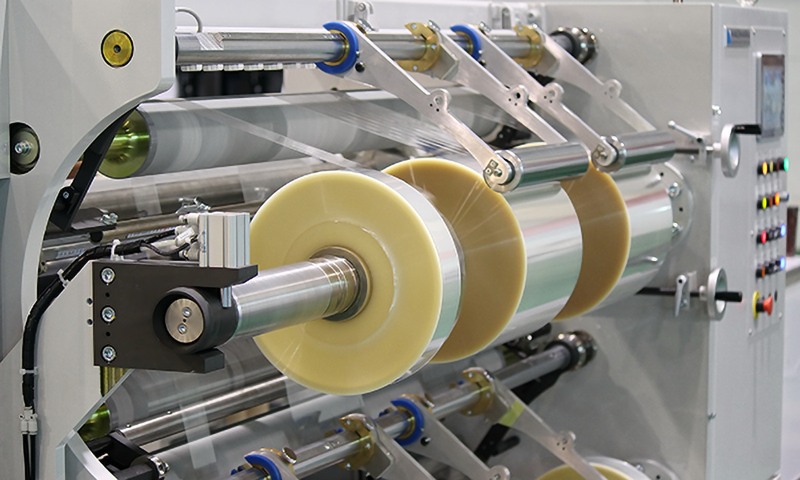
医療分野や自動車部品向けなど、さまざまな業界で使われているフィルム製品。品質の高いフィルムの製造には、スリッター(切断機)による精密な裁断が欠かせませんが、そこで課題となっているのが静電気による品質不良の発生です。
この記事ではフィルム業界における、フィルムの裁断工程でのお困りごとをご紹介します。
フィルムの裁断工程の課題
従来フィルム製品は、幅の広いフィルムロールの原反から、ユーザーの用途に合わせて裁断されています。裁断にはスリッター(切断機)が使われ、巻き出しされたフィルムシートがスリッターを通過し再び巻き取られることで、所定の幅に裁断されていきます。
しかし原反から巻き出しされる際の「剥離帯電」や、スリッターを通過する際の「摩擦帯電」によって静電気が溜まり、さまざまな問題が発生していました。
静電気によって発生する問題
・フィルムの蛇行による巻き乱れ
・フィルム搬送時の作業者への電撃
・ホコリの吸着や異物混入
スリッター装置内ではフィルムが高速で通過するため、静電気の発生が避けられません。
現場では「フィルムをきれいに巻き取りたい」「作業時の電撃をなくしたい」「ホコリの付着をなくしクリーンな製品をつくりたい」との声が上がっていました。
POINT課題のポイント
- 静電気による巻き乱れで困っている
- 静電気による電撃をなくし、安全に作業を行いたい
- 静電気による異物混入で困っている
フィルムの帯電を「イオナイザー」で解決
フィルムの巻き出しの際に発生する静電気は、数十キロボルトと非常に高圧。帯電が装置の制御に影響を与え、誤作動の原因となることもあります。またスリッターの刃物に切断屑を寄せつけてしまい、カットの寸法精度や仕上がりに影響してしまうことも。
そこで採用されているのが「イオナイザー」です。
巻き出し・断裁・巻き取りの各工程にイオナイザーを設置することで、スリッター加工時の静電気を除電することができます。
巻き出し工程
バー型イオナイザー「ACパルス・イオンバー〈Cシリーズ〉」を使い、剥離するフィルムを除電。豊富なサイズから、フィルム原反の幅や装置の幅に合わせて選べます。
イオナイザーをフィルムに近接させることで、イオンバランスが自動調整され、精度の高い除電が可能です。
断裁工程
バー型イオナイザー「静電気除去ハイパワーバー〈HPBシリーズ〉」を使い、断裁中のフィルムを除電。刃物への切断屑の付着も防止します。
バー断面サイズが小さいため、スリッターの狭い装置内でも設置が可能です。
巻き取り工程
ファン型イオナイザー「静電気除去クロスフローファン〈CF-600/CF-300〉」を使い、巻き取り前のフィルムや、巻き取り後のロール全体にイオンを送風。巻き乱れや作業者への帯電を防止します。
高機能フィルムの除電で、現場の生産性向上におこたえします。
POINT解決のポイント
- 静電気による巻き乱れがなくなり、生産性が向上
- 静電気による電撃がなくなり、作業が効率化
- 静電気による異物混入がなくなり、品質向上が実現
関連商品
お問い合わせフォーム
本記事についてのお問い合わせは、下記のフォームからご連絡ください。
課題解決事例は課題解決のための皆様の「気付き」となればと考えています。更なる改善案などがございましたら是非とも共有させていただきたいと存じます。
掲載に関しては都度、ご確認の上追加掲載させていただきます。