【課題解決】高機能フィルムの静電気除去で品質向上が実現
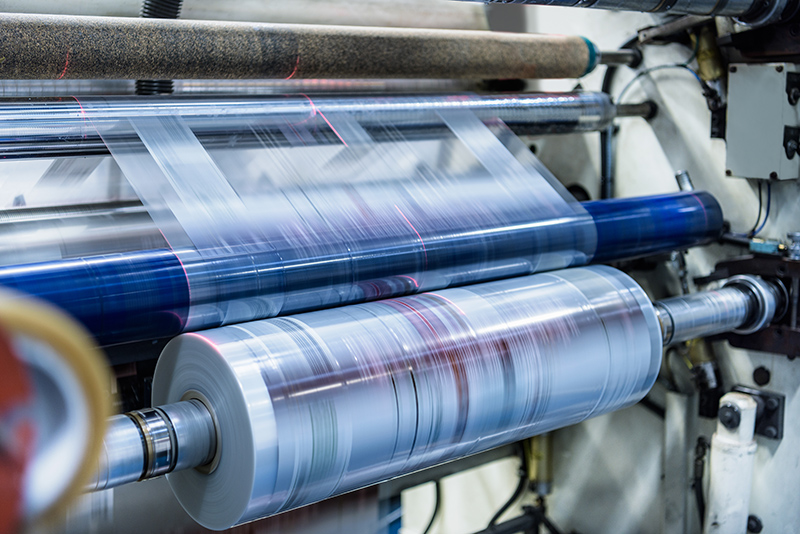
医薬品や食品包装など、さまざまな業界で使われている「高機能フィルム」。酸化やガス透過を防ぐなど、機能性を持った特殊フィルムですが、その印刷工程では高い品質が求められています。
この記事では印刷業界における、高機能フィルムの巻き出し・巻き取り工程のお困りごとをご紹介します。
フィルムの巻き出し・巻き取り工程の課題
従来高機能フィルムの連続印刷やラミネート工程では、高速で走行するフィルムが装置内のローラーを通過し、巻き出し・巻き取りを行います。
フィルムには高いテンション(張り)がかかっているため、複数のローラーを通るうちに摩擦や剥離を繰り返しながら帯電し、高い電圧が蓄積します。
そのため静電気によるホコリの吸着で異物が混入したり、蛇行による巻き取り不良や印刷不良が起こることも… フィルムの交換時に、作業者に電撃が発生することも大きな問題となっていました。
ある工場では「静電気を抑えるために工場内の湿度を上げているが、湿気で印刷物がだめになってしまう」などのお困りも。
現場では「異物混入による検品をなくしたい」「巻き直しのムダをなくしたい」「電撃をなくし安全に作業がしたい」などの声が上がっていたのです。
POINT課題のポイント
- ・静電気による異物混入で困っている
- ・静電気による巻き取り不良で困っている
- ・静電気による電撃をなくし、安全に作業を行いたい
フィルムの帯電を「バー型イオナイザー」で解決
フィルムの連続印刷で発生する静電気は、数十キロボルトと非常に高圧。作業者へ放電してしまうとショックで転倒し、大きな事故にもつながりかねません。また巻き取りエラーによる機械停止も、生産性に大きな影響を与えてしまいます。
これらの静電気は一部をイオナイザーで除電しても、帯電を繰り返すため大きな効果は見込めません。
そこで採用されているのが「バー型イオナイザー」です。
「静電気除去ハイパワーバー〈HPBシリーズ〉」は、豊富なサイズから選べるバー型のイオナイザー。フィルムの幅に合わせたイオナイザーを工程内に設置し、帯電量が増える前に除電することで、フィルムへの帯電を確実に防止することができます。
また帯電量が大きな場合には、高圧電源内蔵の「静電気除去ACパルス・クリーンバー〈Cシリーズ〉」。装置内の狭い隙間には、電源別置きのスリムな「静電気除去イオンバー〈SLシリーズ〉」がおすすめ。シート巻き取り部には「静電気除去クロスフローファン〈CF-600〉」、「静電気除去3ファン〈L-90〉」を使うと設置が簡単です。
高機能フィルムの静電気除去で、現場の品質向上におこたえします。
POINT解決のポイント
- ・静電気による異物混入がなくなり、品質向上が実現
- ・静電気による巻き取り不良がなくなり、生産性が向上
- ・静電気による電撃がなくなり、作業が効率化
関連商品
お問い合わせフォーム
本記事についてのお問い合わせは、下記のフォームからご連絡ください。
課題解決事例は課題解決のための皆様の「気付き」となればと考えています。更なる改善案などがございましたら是非とも共有させていただきたいと存じます。
掲載に関しては都度、ご確認の上追加掲載させていただきます。