【課題解決】バンパーゲートカット時の静電気除去で切粉の付着を防止
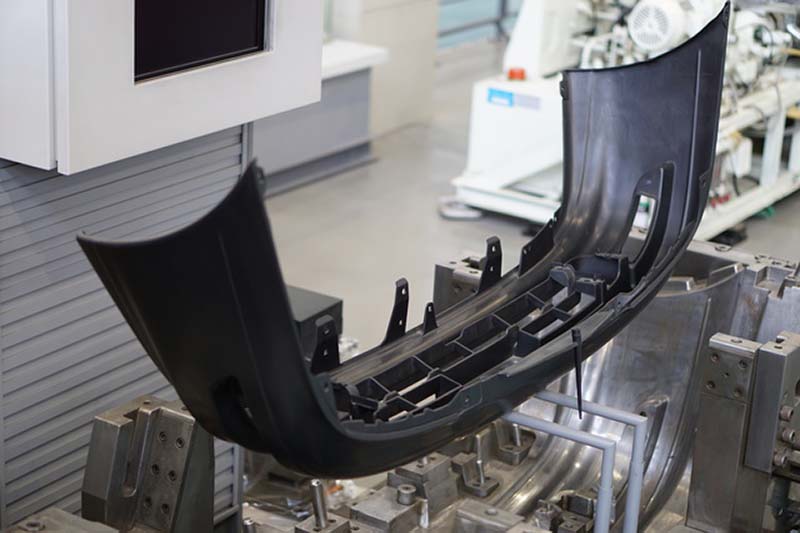
近年自動車のEV化の流れを受けて増加しているのが、樹脂による車体の軽量化ニーズです。なかでも外装部品には、高い強度を持った軽量な樹脂部品の採用が増えています。
この記事ではバンパーなどの自動車樹脂部品の、ゲートカットに関するお困りごとをご紹介します。
ゲートカット時の静電気による課題
サイドゲートによる樹脂成形。樹脂の流れが均一で低コストのため、多くの自動車樹脂部品で採用されている成形方法ですが、そこで課題となっているのがバンパー成形時のゲートカットです。
従来バンパーなどの自動車樹脂部品のゲート処理では、ロボットアームが自動でゲートカットを行います。
しかしゲートカット時に帯電していた静電気によって、空気中の塵埃や切粉がバンパーに付着してしまうことがありました。
切粉の付着した部品を次工程に流してしまうと、塗装やUVコーティングなどの表面処理でブツ(粒)が発生し品質低下の原因に… エアーブローで吹き飛ばしても、塵埃が舞うだけで再付着するため、拭き取り作業を行なっています。
そのため現場では「ゲートカット時の切粉の付着を防止したい」「拭き取りなどの余計な作業をなくしたい」などの声があがっていました。
POINT課題のポイント
- ゲートカット時に帯電した静電気で切粉が付着
- 表面処理でブツ(粒)が発生し品質が低下
- 余計な拭き取り作業をなくしたい
ゲートカット時の切粉の付着を「イオナイザー」で解決
バンパーのゲートカットやパネル部品のバリ取りなど、大型樹脂成形部品の後処理には、エンドミルや円盤カッター、超音波カッターなどが使われます。しかし、これらカッターを使った切断には切粉がつきもので、摩擦による静電気(摩擦帯電)によって切粉の付着など多くの問題が発生しています。
通常はエアーブローを使って吹き飛ばしますが、静電気によって付着した切粉は除去することが難しく、部品の隙間や裏側にまで入り込んだ切粉は、落とすことができませんでした。
そこで採用されているのが「ノズル型イオナイザー」です。
「静電気除去ノズル〈N-1/N-3〉」は、樹脂部品の除電に最適なノズル型のイオナイザー。ゲートカットのロボットアームに搭載しイオン化エアーを吹き付けることで、切粉を飛ばしながら「摩擦帯電」による再付着を防止することができます。
またエアーブローによるカッターの冷却効果で、刃先の寿命向上にもつながります。
ゲートカット時の静電気の除電で、現場の生産性向上におこたえします。
POINT解決のポイント
- ゲートカット時の除電で切粉の付着を防止
- 表面処理のブツ(粒)がなくなり品質向上
- 余計な拭き取り作業がなくなり生産性向上
関連商品
お問い合わせフォーム
本記事についてのお問い合わせは、下記のフォームからご連絡ください。
課題解決事例は課題解決のための皆様の「気付き」となればと考えています。更なる改善案などがございましたら是非とも共有させていただきたいと存じます。
掲載に関しては都度、ご確認の上追加掲載させていただきます。