【課題解決】オフセット印刷の用紙の除電で効率化・品質向上が実現
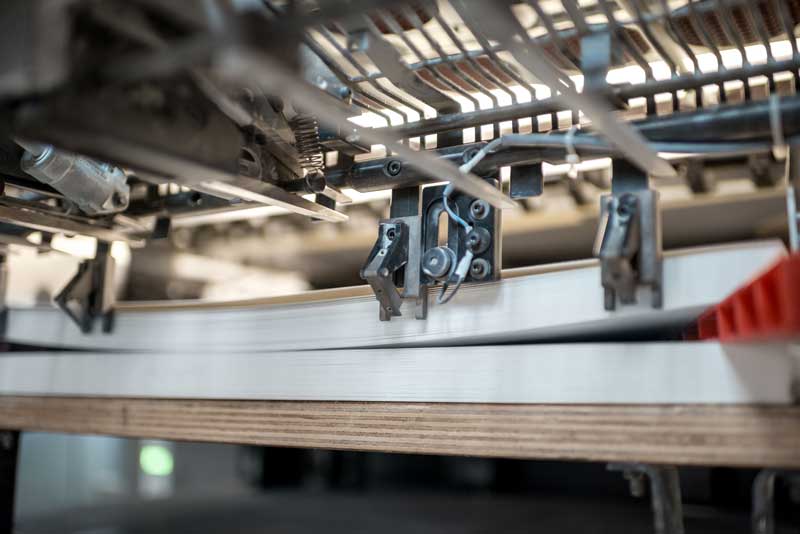
大量印刷に欠かせないオフセット印刷機。近年では人手不足や印刷物のデジタル化も重なり、より効率的でムダのない印刷が求められるなか、課題となっているのが用紙の給紙工程です。
この記事ではオフセット印刷工場における、用紙の給紙に関するお困りごとをご紹介します。
オフセット印刷の給紙工程の課題
従来厚めのオフセット印刷では、あらかじめA版や菊版サイズにカットした用紙を作業者が「供給装置」に置き、積み上げていきます。
しかし供給装置が用紙をピックアップして送る際、剥離帯電によって静電気が発生。用紙どうしが付着し二枚取りや、静電気によるインクの跳ね・にじみなどが発生していました。用紙が静電気を帯びていると、工場内を浮遊している微小なゴミやホコリが付着してしまい、そのままインキを乗せてしまうと印刷不良の原因にもなります。
また帯電した用紙どうしが反発してしまい、用紙の不揃いが発生… ストッカー内でバラバラになってしまい、後工程に影響してしまうこともありました。
現場では「いかに静電気による印刷不良をなくし、印刷の品質と効率を上げるか」が課題となっていたのです。
POINT課題のポイント
- 二枚取りによる紙詰まりをなくしたい
- インクの跳ねやにじみによる印刷不良をなくしたい
- 印刷後の用紙をきれいに束ね、後工程の手間をなくしたい
オフセット印刷時の帯電を「イオナイザー」で解決
一般的にオフセット印刷時の除電には「除電ブラシ」が使われています。除電ブラシは、用紙とブラシの間の電位差を利用し放電吸収する導電性のブラシですが、電位差が小さい場合、空気中の分子をイオン化することができず表面の静電気を除去しきることができません。
そのため「除電ブラシは付いているけど、実際に役に立っているかわからない…」といった声も多く聞かれます。
そこで採用されているのが「イオナイザー」です。
給紙・印刷・排紙(ストッカー)の各工程にイオナイザーを設置することで、印刷品質を改善し効率アップさせることができます。
給紙工程
ノズル型イオナイザー「静電気除去ピンポイントノズル〈N-3〉」を使い、重なった用紙の隙間にイオン化エアーをブロー。用紙をさばきながら除電することで、二枚取りを防止します。
印刷工程
バー型イオナイザー「静電気除去ハイパワーバー〈HPBシリーズ〉」を使い、印刷直前の用紙を除電。用紙は高速走行しているため、ベルトやガイドロールとの間で摩擦帯電が起こりやすく、イオナイザーを用紙に接近させ2本並列でイオンを供給するなど、強力な除電が求められます。
排紙工程
バー型イオナイザー「ACパルス・イオンバー〈Cシリーズ〉」を使い、排紙直後の用紙を除電。ストッカーに積み重なる前に除電することで、印刷後の用紙のバラつきを防止します。
オフセット印刷の用紙の除電で、現場の生産性向上におこたえします。
POINT解決のポイント
- 二枚取りによる紙詰まりがなく、生産性が向上
- インクの跳ねやにじみがなくなり、品質が向上
- 印刷後の用紙がきれいに束なり、後工程の手間がなくなる
関連商品
お問い合わせフォーム
本記事についてのお問い合わせは、下記のフォームからご連絡ください。
課題解決事例は課題解決のための皆様の「気付き」となればと考えています。更なる改善案などがございましたら是非とも共有させていただきたいと存じます。
掲載に関しては都度、ご確認の上追加掲載させていただきます。