【課題解決】パーツフィーダー搬送時の静電気除去でチョコ停を防止
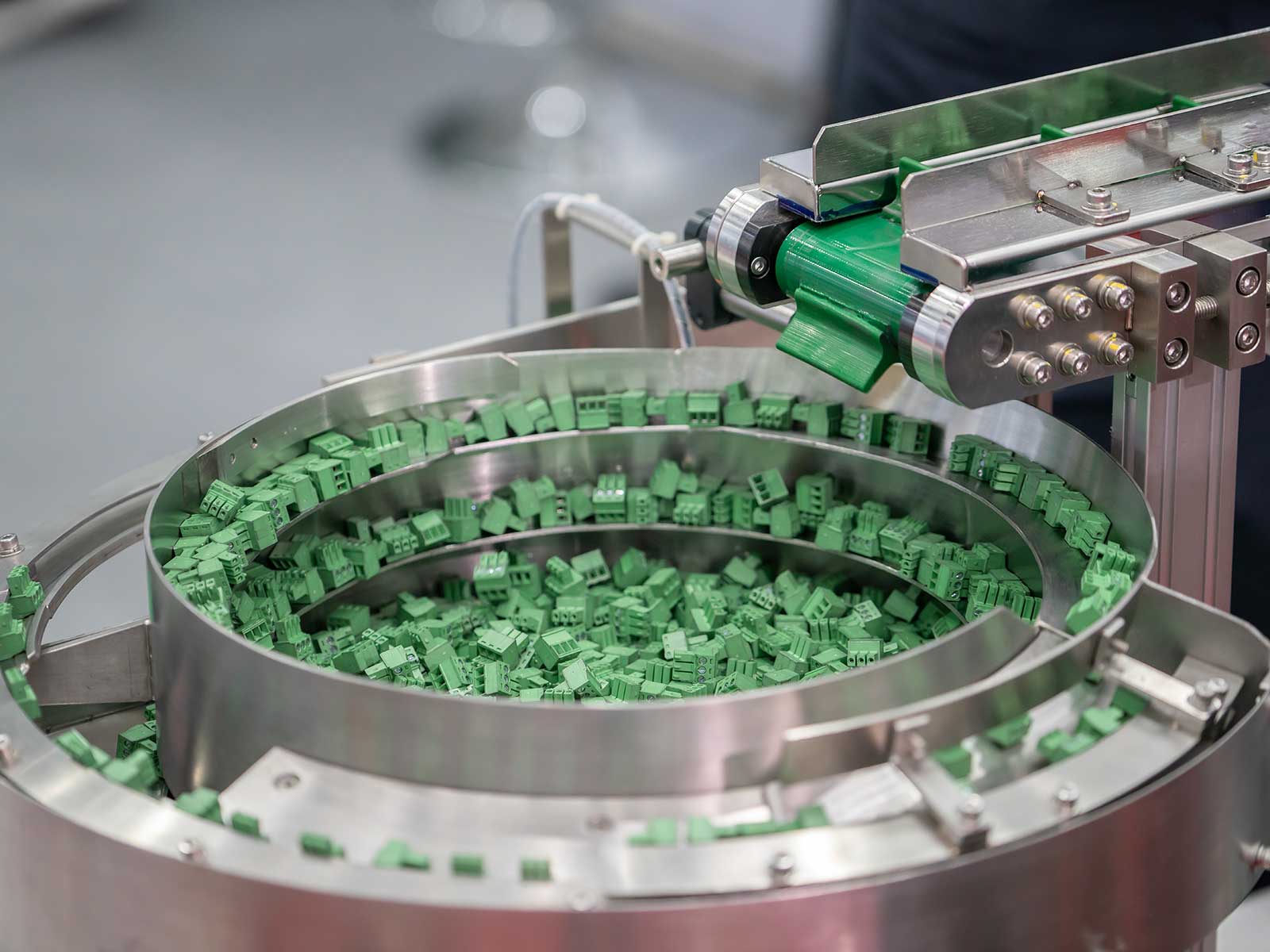
生産ラインの部品供給で使われる「パーツフィーダー」。大量の部品をボウル内で振動させ部品を供給する自動化に欠かせない装置ですが、部品の小型化にともない静電気によるチョコ停が問題となっていました。
この記事では電子機器の部品実装における、パーツフィーダーによる搬送工程のお困りごとをご紹介します。
パーツフィーダーによる搬送工程での課題
近年、電子機器や電子回路の小型化にともない使用される電子部品も小型・軽量化、課題となっているのが部品供給時の静電気対策です。
従来電子機器の実装工程では、パーツフィーダーを使い部品を供給し実装していきます。
しかしパーツフィーダーのボウル内の振動により、部品が接触・剥離・摩擦を繰り返すことで帯電してしまい、周辺のホコリを引き寄せたり、部品どうしがくっつきチョコ停(搬送不良)が発生することがありました。帯電したまま部品を搬送してしまうと、後工程で加工不良の原因になることも…
Oリングやスペーサーなどの薄い小物部品は、重量のわりに表面積が大きく、わずかな帯電であってもパーツフィーダに吸着してしまい部品詰まりを起してしまいます。
またこれらの部品はシリコンやPP・PEなどの絶縁体が多く、摩擦によって帯電しやすい傾向にあります。
現場では「パーツフィーダーのチョコ停をなくし、生産性を上げたい」「ホコリの付着など、不良品の混入を防ぎたい」との要望がありました。
POINT課題のポイント
- パーツフィーダー搬送時の帯電で困っている
- 帯電によるチョコ停をなくしたい
- 帯電による不良品の混入をなくしたい
パーツフィーダー搬送時の帯電を「静電気除去ファン」で解決
パーツフィーダーの静電気対策には「静電気除去装置」が用いられますが、長時間稼働していると、突然部品が詰まりチョコ停が起こることがあります。
実はその原因はイオンバランス。イオンバランスが悪いと、イオンで中和させたはずの部品が逆に帯電してしまうのです。現場でも「静電気除去装置を使っても、しばらくしてからチョコ停が起こる!」といった声がありました。
そこで採用されているのが「静電気除去ファン」です。
「静電気除去ファン〈F-120R/F-6RCL〉」は、イオンバランスに優れた圧電高周波ACタイプのファン型イオナイザー。独自設計のイオン生成コントロールで、長時間の稼働でもイオンバランスが崩れず、パーツフィーダーの除電に最適です。
ボウル上からパーツフィーダー全体に向けてイオンエアーをブローすることで、部品どうしの帯電をなくし突然のチョコ停を防ぐことができます。
また帯電量が多く静電気を除去しきれない場合は、レール上の部品を狙って除電ができる、「静電気除去ノズル〈N-1/N-3〉」の併用がおすすめ。設置場所を選ばない軽量・コンパクトサイズで、部品のスポット除電に最適です。
パーツフィーダーの静電気によるチョコ停をなくし、現場の生産性向上におこたえします。
●ここがポイント
パーツフィーダーのボウルは、防錆・腐食防止のためアルマイト処理が施されていることがありますが、アルマイトは絶縁体のため帯電しやすくチョコ停の要因となります。
確実な除電のためにも、サンドブラストによるアルマイトの除去や導電性のコーティング剤も検討しましょう。
POINT解決のポイント
- パーツフィーダー搬送時の帯電を防止
- 帯電によるチョコ停がなくなる
- 帯電による不良品の混入がなくなる
関連商品
お問い合わせフォーム
本記事についてのお問い合わせは、下記のフォームからご連絡ください。
課題解決事例は課題解決のための皆様の「気付き」となればと考えています。更なる改善案などがございましたら是非とも共有させていただきたいと存じます。
掲載に関しては都度、ご確認の上追加掲載させていただきます。